3D-printing "error" used to produce high-tech textiles
Posted: 30 Oct 2020, 15:40
If a 3D printer leaves gaps in the plastic that it deposits, it's usually thought of as an unwanted flaw. Now, the process has been harnessed to quickly and cheaply produce pliable polymer textiles.
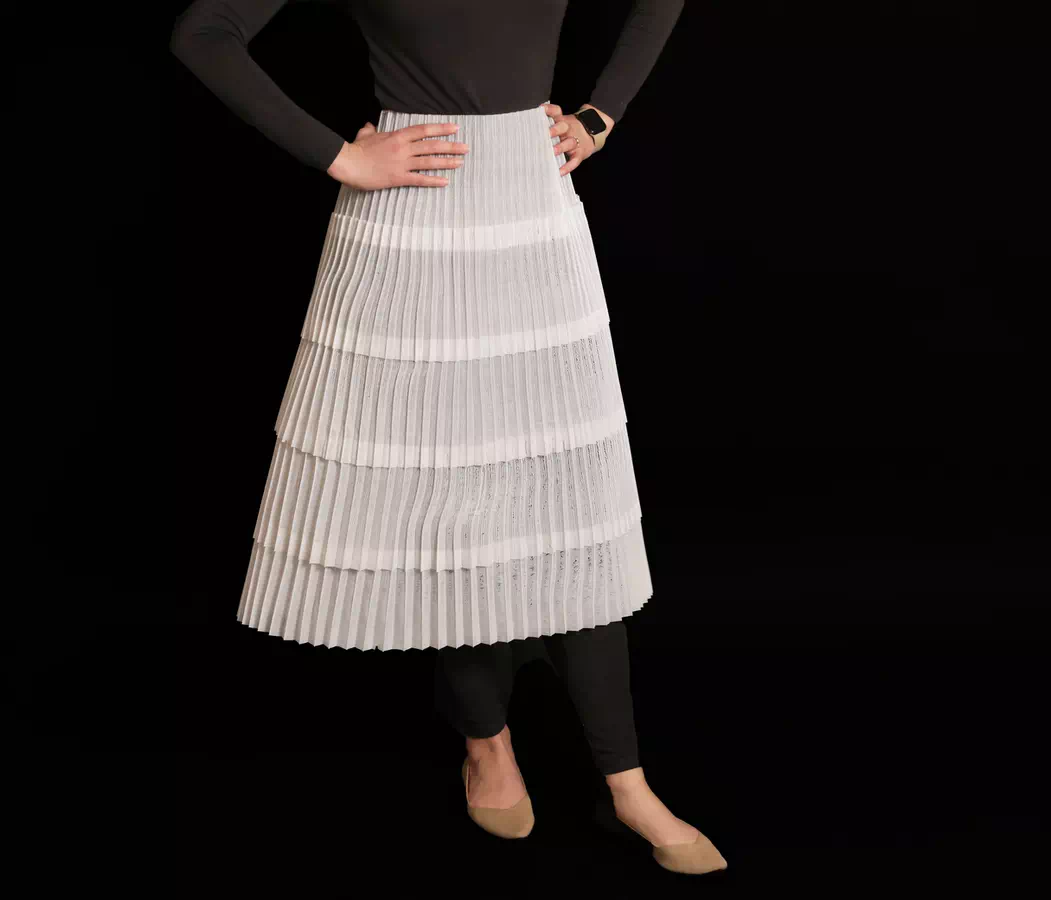
Ordinarily, commonly used fused deposition modelling (FDM)-type printers create items by extruding successive layers of molten plastic. Once the layers of deposited plastic have cooled and fused together, they form a hardened solid object.
Sometimes – due to a flaw in the printer or the programming – not enough plastic is extruded. This is known as under-extrusion, and it results in the finished product being full of small gaps.
MIT Media Lab grad student Jack Forman decided to put that error to use, creating a program that causes off-the-shelf, inexpensive FDM printers to under-extrude in a precise and controlled "glob-stretch" pattern – the latter is made up of tiny polymer plastic pillars linked together by thin polymer strands.
The resulting "DefeXtiles" have a tulle-like quality, in that they take the form of a fine, flexible netting.
Among other things, Forman and colleagues have so far used the technology to create items such as full-sized skirts, translucent lace sheets, a roll of fabric long enough to stretch across a baseball diamond, and an electronically conductive lampshade with pleats that can be pinched together to turn on the lamp.
Other applications could include the creation of surgical mesh with tuneable mechanical properties, along with prototyping and customization in the fashion industry.
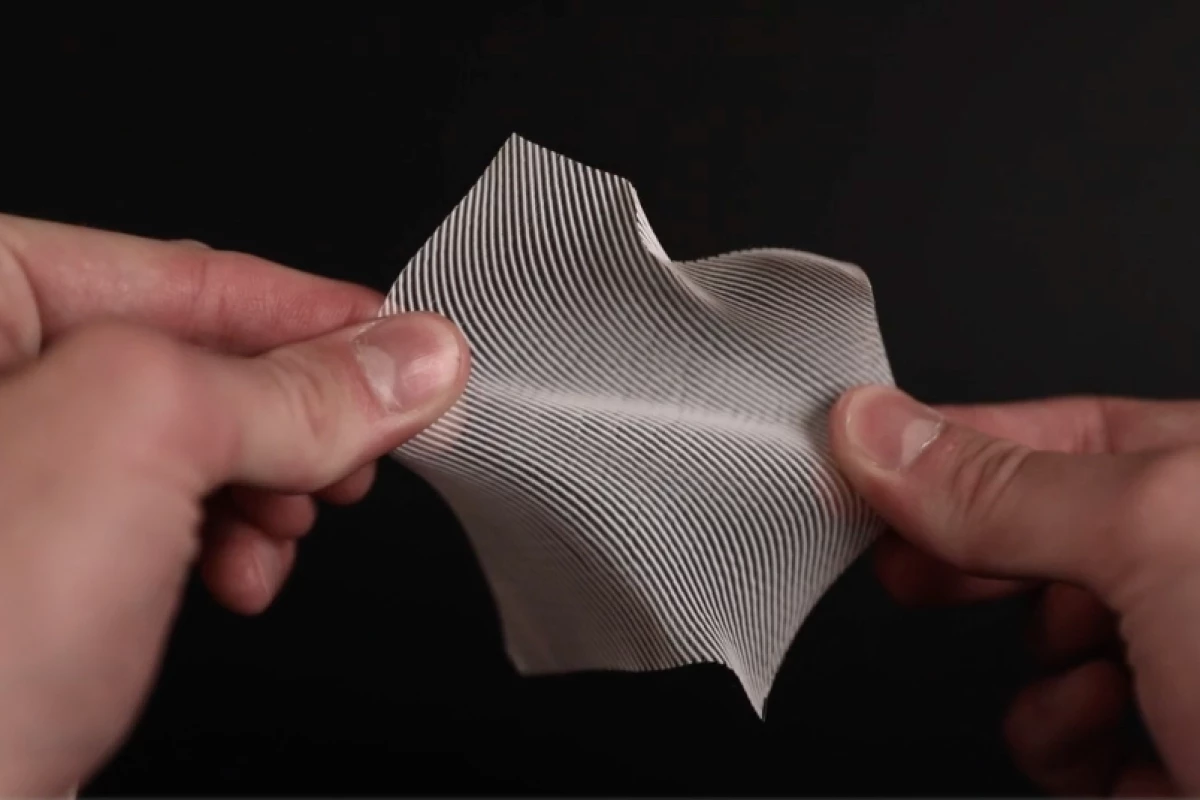
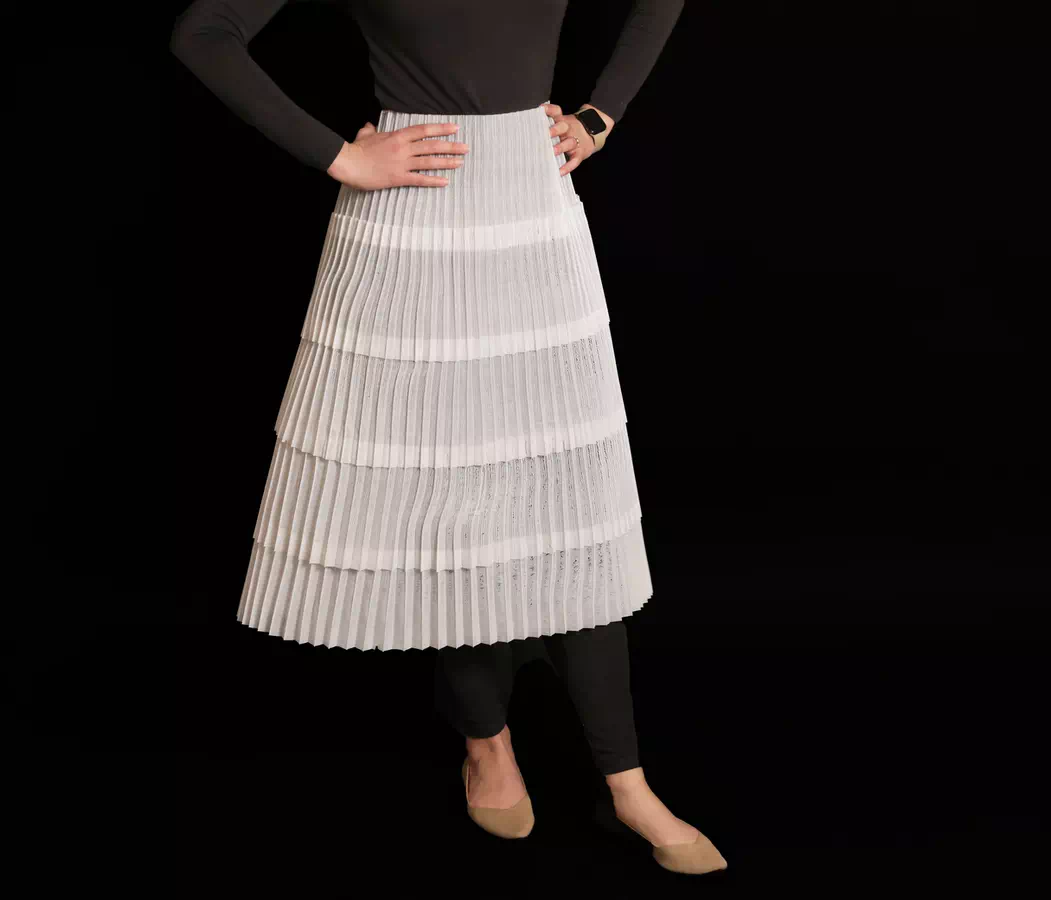
Ordinarily, commonly used fused deposition modelling (FDM)-type printers create items by extruding successive layers of molten plastic. Once the layers of deposited plastic have cooled and fused together, they form a hardened solid object.
Sometimes – due to a flaw in the printer or the programming – not enough plastic is extruded. This is known as under-extrusion, and it results in the finished product being full of small gaps.
MIT Media Lab grad student Jack Forman decided to put that error to use, creating a program that causes off-the-shelf, inexpensive FDM printers to under-extrude in a precise and controlled "glob-stretch" pattern – the latter is made up of tiny polymer plastic pillars linked together by thin polymer strands.
The resulting "DefeXtiles" have a tulle-like quality, in that they take the form of a fine, flexible netting.
Among other things, Forman and colleagues have so far used the technology to create items such as full-sized skirts, translucent lace sheets, a roll of fabric long enough to stretch across a baseball diamond, and an electronically conductive lampshade with pleats that can be pinched together to turn on the lamp.
Other applications could include the creation of surgical mesh with tuneable mechanical properties, along with prototyping and customization in the fashion industry.